NickMaul
Well-Known Member
- Joined
- Jul 4, 2009
- Location
- Norfolk, VA
Welp the dana 300 fought me pretty hard. I paid the price on a few things by rushing. Definitely learned a lesson when assembling stuff like that but fortunately was able to correct them.
The only thing I am still unsure of if the detent spring pressure on the rear output shift rail. I purchased the JB Conversions detent spring and ball kit and followed the instruction. The force to push and pull the shift rails definitely isn't even but I am willing to try running in and if it doesn't work well I will have to go back to the drawing board. Everything else feels really good.


So the ax15 came from a YJ. Wrangler AX15s are clocked higher than cherokee AX15s. With the clocking ring on its lowest position the dana 300 is about an inch or two above the bottom of the frame rails. I took a razor to the rust prevention plan supplied by 4.0 valve cover/rear main seal oil leak and exposed my sheet metal like a surgeon. Then the hammer came to play. I definitely need to smooth the sheet but it gained me the clearance that I need.


Driveshaft clearance is going to be interesting. May have to get some hammer treatment on the floor board also

The only thing I am still unsure of if the detent spring pressure on the rear output shift rail. I purchased the JB Conversions detent spring and ball kit and followed the instruction. The force to push and pull the shift rails definitely isn't even but I am willing to try running in and if it doesn't work well I will have to go back to the drawing board. Everything else feels really good.


So the ax15 came from a YJ. Wrangler AX15s are clocked higher than cherokee AX15s. With the clocking ring on its lowest position the dana 300 is about an inch or two above the bottom of the frame rails. I took a razor to the rust prevention plan supplied by 4.0 valve cover/rear main seal oil leak and exposed my sheet metal like a surgeon. Then the hammer came to play. I definitely need to smooth the sheet but it gained me the clearance that I need.


Driveshaft clearance is going to be interesting. May have to get some hammer treatment on the floor board also


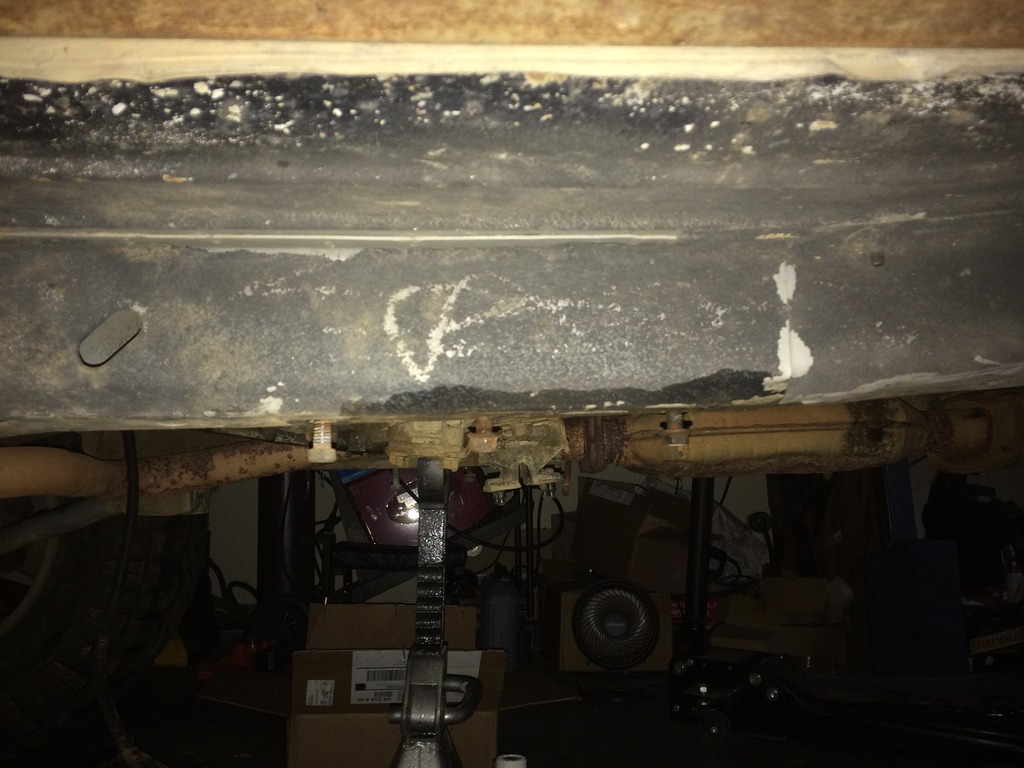
Last edited: