Tech11
Well-Known Member
- Joined
- Dec 7, 2007
- Location
- Greensboro
Okay, lets start off and get this out front, I'm a TAD eccentric when it comes to some things.
In my LJ switch panel I've swapped in 2 Cherokee fog lamp switches for my future offroad lights and rock lights (I wanted a clean look)
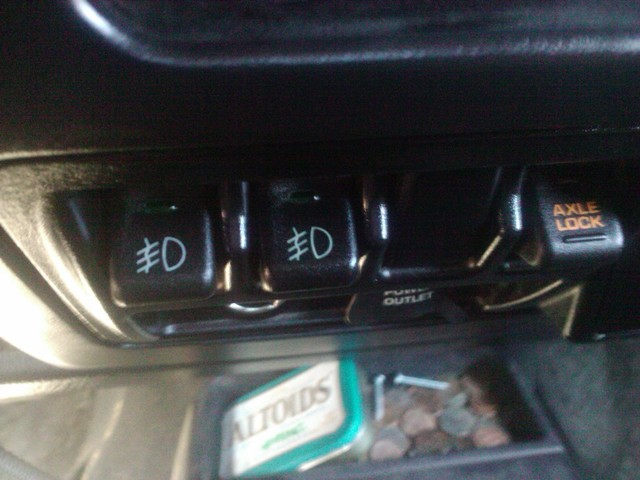
In looking around at various projects I found an extended idle switch from the police package Cherokees.
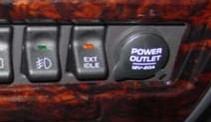
When wired up correctly it will bump the associated police packaged 4.0 idle up to about 1000ish rpm, it was for running police lights and all the extra police "stuff".
1000 RPM isn't really much of a bump for anything that I have in mind, mainly winching.
So from what I've read on this switch, it looks like I would have 2 wires to play with, which should give me a 12v signal (+/-)
I've not messed with RC stuff/servos and the likes in years, but just poking around a few sites it looks like I SHOULD be able to wire up a servo with an arm, and once it receives the signal from this switch with appropriate adjustments I could have it pull the throttle back and idle at whatever RPM I finally adjust the servo to pull to.
Yeah, hand throttle, sure, but this is just how I do things sometimes. I'm really looking for input on making this work. Or maybe pitfalls or something I'm overlooking.
I'm thinking servos because I'm not really sure about solenoids, I was thinking servos would be simpler, well more simple in this rube goldberg contraption.
waterproof high torque servo most likely?
or is this just crazy?
In my LJ switch panel I've swapped in 2 Cherokee fog lamp switches for my future offroad lights and rock lights (I wanted a clean look)
In looking around at various projects I found an extended idle switch from the police package Cherokees.
When wired up correctly it will bump the associated police packaged 4.0 idle up to about 1000ish rpm, it was for running police lights and all the extra police "stuff".
1000 RPM isn't really much of a bump for anything that I have in mind, mainly winching.
So from what I've read on this switch, it looks like I would have 2 wires to play with, which should give me a 12v signal (+/-)
I've not messed with RC stuff/servos and the likes in years, but just poking around a few sites it looks like I SHOULD be able to wire up a servo with an arm, and once it receives the signal from this switch with appropriate adjustments I could have it pull the throttle back and idle at whatever RPM I finally adjust the servo to pull to.
Yeah, hand throttle, sure, but this is just how I do things sometimes. I'm really looking for input on making this work. Or maybe pitfalls or something I'm overlooking.
I'm thinking servos because I'm not really sure about solenoids, I was thinking servos would be simpler, well more simple in this rube goldberg contraption.
waterproof high torque servo most likely?
or is this just crazy?